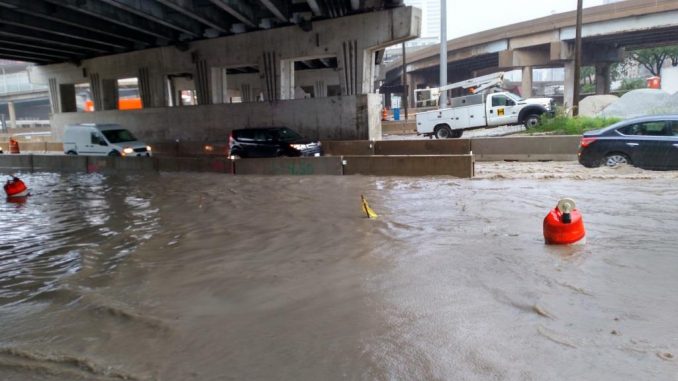
It was simply one of those days.
A small crisis to navigate. Several problems to solve. Critical thinking tested. Read & react.
The NOAA weather station at Midway Airport recorded 2.17 inches of rain today. It fell on Chicago in a span of about 5 hours.
What happens to a Resident Engineer working on a construction site that gets hit with 2.17 inches of rain….? Well, it means you are likely going to have a busy day. Go ahead, let your mind wander for a second…..whatever thoughts just ran through your head are probably correct. Water + Construction = Issues.
I spent today battling Mother Nature, a construction site and my own mind. And now, as I sit in my dining room with a Blue Moon sitting to my left, it’s time to let today’s ordeal become a debriefing, a textbook “Lessons Learned” article. I drove home from the site with Evernote running on my phone, clicking the Talk-to-Text button dozens of times. A bunch of things went right today, a few things went wrong, and opportunities for improvement were plentiful. Open up your toolbox and dive into this article, everything I have on my workbench is free for the taking….
The Project
So my current deployment has me working on the Eisenhower Expressway in Chicago. Our crew is involved with a $30 million roadway reconstruction project that is one “small” contract associated with the rehabilitation of the Circle Interchange. $30 million sounds like a pretty big job, but in reality, it’s really not: Roadway reconstruction, a few retaining walls, multiple MOT stages, sewer & electric – Boring by my standards.
Today started as a normal, run-of-the-mill kind of day: Rain was in the forecast. The Contractor ended up cancelling several operations, so it had all the makings of a paperwork catch-up day.
Hmmm…sounds too easy, right?
So I’m posted-up in my truck updating my diary at around 0800 hours. Shearrisa, our IDOT Resident Engineer called to check-in. She asked if it was raining downtown yet: No, not yet. She said it was pouring in the south suburbs and was surprised that we hadn’t gotten hit yet.
Not too long after we hung up, the rain started. I was on the east end of our project and, after about a half hour of steady rain, I noticed that we were getting quite a bit of runoff from the adjacent job to our south. And then I noticed it.
Holy Cripes. Ramp ES was taking on water.
The Shyt Hit the Fan
What seemed to happen in an instant, the ramp that takes the eastbound Eisenhower Expressway to the southbound Dan Ryan Expressway was flooding. Water was flowing overland from all directions. In the low area under the Halsted Street bridge, we had a combination of newly-installed sewer in the same area as some existing sewer. The water was gaining ground on us in, what seemed like, a matter of minutes. Before I knew it, the entire ramp was covered with water.
What the hell is going on? Or not going on, in this case?
My first call was to the Contractor’s superintendent: In my usual sarcastic fashion, I asked him if he brought his Big Boy Pants to work today because I was about to challenge him: The ramp is flooding, and it needs to get un-flooded and he needed to spring into action.
This is real – It’s gonna be a long morning….
Knowledge
Engineers love to solve problems. But most of the time, if you are a Resident Engineer like me, or working as a construction engineer, the problems we solve are on paper. They are mind jumbles that don’t necessarily require brawn, they need our brains. And typically we look to the Contractor to execute the actual hand-on efforts, taking our problems on paper and turning them into tangible solutions. But today’s efforts challenged me on both fronts: The Contractor didn’t have any staff who was intimately familiar with this area of the site. And because I was first on the scene and not afraid of getting my hands dirty, I pretty-much turned into the de-facto Incident Commander. By default, those Big Boy Pants I asked the Contractor’s superintendent about ended up hanging off of my suspenders this morning….
The problem statement was easy: Get rid of the water. The path to success wasn’t so clear. In fact, it was hidden under a few feet of murky, silt-laden storm water.
Commander’s Intent
So somewhere under the murky water lied both a proposed sewer system AND an existing system. The proposed system had a tie to the existing system. There were numerous existing drainage structures that “should” have still been actively working. Where were they? Open or closed lids? Under the murky water: Are the grates clogged? What about the inlet filters? Where the hell are they? I KNOW the temporary connections that we made on the other side of the expressway hooked-up properly – Are they clogged? Is there too much surge somewhere that is back feeding into our low spot?
Information overload. Critical thinking. Calm under pressure.
My initial attack meant trying to find the drainage structures that I remember seeing. Therein lied a big part of the diagnosis problem: I was in the blind. Where are the existing catch basins? I can’t see anything.
Flying solo for a bit with sewer pick in-hand, I started pinging the pavement in the water, trying to find a lid. After a few minutes, a couple of the Contractor’s laborers showed up. They were guiding me towards one of the structures that we had installed. Tapping, looking, listening to the guys…and then out of nowhere – WHOA!!! Down Goes Frazier!!! (almost…)
I ended up stepping off the edge of the pavement which I obviously couldn’t see under the murky water, and found myself in belly-button deep water. OK, now the game has changed. Wet boots happen now and again, but wet boxer shorts are a much rarer occurrence. Now this gig is getting real. (Glad I left my wallet in my truck, by the way…..).
All this time while searching, I’m thinking about the vehicles. How bad is the traffic backup? What happens if we get a stall in the lane? Does the Comm Center know what’s going on? Fortunately, vehicles were getting by us. The ramp is superelevated, and so long as people stayed on the high side of the ramp, they traversed the water without an issue. We were very fortunate that we didn’t have any vehicles stall-out. Score one for good fortune. One less thing to worry about.
With soaking wet plans in-hand and a lot of walking in thigh-deep water, the laborers & I managed to find a couple of structures that had connecting laterals to one of the active outfalls. The Contractor’s foreman, Danny, had his phone pretty-much glued to his head as he called his equipment suppliers to try to free-up a trash pump and enough hose for us to pump to an active catch basin. We should have gravity flow right now but we obviously don’t. Something isn’t right….
We had the good-fortune of our neighboring Contractor, Judlau, jumping in and helping us, loaning a 3″ pump and hoses to get us going. That would be the ticket we needed punched right now. Hat-tip goes out to Jason Lang from Gonzalez and John Carroll from Judlau for battling with us & providing us with some mutual aid.
After about an hour of moving gear around, we managed to fire up the pump. Watching the pump-out going into a catch basin and not seeing it puke back out at us was like buying a winning scratch-off ticket – Water level dropping. Ramp lane clearing. Mission soon to be accomplished.
Diagnosis
X-ray vision not one of my Super Powers, so without being able to see under ground, I have to go with my gut, but this one is pretty easy to predict – The likely culprit was a clog in the line, somewhere. Being in the low spot, and not knowing the maintenance history of the drainage system, this area gets a lot of action. It’s a construction access point, so it gets exposed to tire flash all the time. About a month ago, there was quite a bit of sewer work in the area. We really don’t have a lot of exposed, non-stabilized areas but we are surrounded by trench backfill and aggregate, but water moves shyt around, like it or not. Lots of ingredients to a messy recipe.
There were inlet filters in the structures, which was good, but they were inundated during the storm. I left the site after we got the water pumped down and was able to probe the basins – I can feel sediment in the sumps, the eastern-most structure felt like it was full to the top with sediment. It’s totally reasonable to assume that the piping system is sediment-laden too. We had, probably, 6 feet of head at the peak of the flood, so you would think that would be enough head to help self-cleans the system, but obviously, something in the run is clogged. We’re putting into motion getting the Contractor to vac & televise the system. I plan on getting inverts of the pipe runs as well, just to see what we’re dealing with.
Lessons Learned
As I was driving home, sitting in my completely soaked-to-the-bone threads, I told myself that I ABSOLUTELY HAD to put together a debrief of today’s events. We learn from our experiences and our mistakes. Here are some of my take-aways:
1. Plan for the 100-Year Event Hitting Your Site – Because It Will Hit
Mother Nature doesn’t play games. She rears her head when you least expect it. You need to plan for her showing up when you don’t want her to because I guarantee when she get there, she will make your life hell.
I get a lot of grief from folks who believe that I think too much, that I’m a glass-half-empty kind of guy who just likes to look for problems when there aren’t any.
Nope. Wrong.
Part of becoming a seasoned RE is understanding that the shyt is gonna hit YOUR FAN sooner than you think. If you want to walk around your jobsite smelling roses and looking up at a sunny sky everyday, you picked the wrong profession. Things can go goes sideways EVERYDAY and you need to be ready for it.
Pre-plan. Look ahead to the next 3 moves. Strategize about what can happen. What WILL happen.
When it comes to lousy weather, understand that no matter who you are or where your job is, water, in some form, is going to try to kick your ass. Rain. Snow. Ice. Runoff. You are going to have the Mother-of-All-Storms hit your site. Are you ready?
2. Know Your Drainage System Inside & Out
You’ll recall my series of articles on Job Size Up and Job Pre-Construction Document Reviews where we discussed building the job in your mind before you put your first shovel in the ground. Let me tell you something – In a crisis, you will be testing how well you studied the plans. And understand that this test isn’t going to be a 10-question quiz, this is going to be a multi-hour final exam for you.
I had a solid understanding of the drainage systems, both existing & proposed, but my understanding wasn’t 100%, I was at 95%: That’s not good enough. I wasn’t the day-to-day inspector on the install, but I had a pretty good sense of the lay-of-the-land. I had enough of an understanding to be able to think through a couple of options for vacating the water. Our neighboring contractor & RE staff gave us a couple of other potentials. I put all that knowledge, though not perfect, and devise a course of action. I’d give myself a B- on the test. I didn’t deserve to get A+ that I wanted….
You have got to know your systems. Inside & out. You have got to take the time to study. You might think you know where things are at: Try doing it with a blindfold (that being silt-laden stormwater) in a driving rainstorm and see how you perform. Separate the men from the little boys (and girls…). I can’t stress enough how important it is as a Resident Engineer, to truly understand the battlefield that you are working on.
3. Focus on Low Points
It sounds so obvious it’s stupid, but it is 100% truth: Low points are the entry-points to your outfalls – Do you know where they go? Are they functional? Are they clean? Are they connected?
You know, it’s easy for any of us to make a site run on a warm, sunny day when nothing is going wrong. Try this: Challenge yourself. What happens when the rains come tomorrow? Do you know where the water is going to go? Don’t pretend. Don’t puff out your chest and think that you have it all figured out already. Don’t think that your sewer inspector and the contractor took care of everything during the install: You might end up becoming the Incident Commander. Challenge yourself. Think through scenarios. Play mind games with yourself. Walk the job with a purpose. Look for opportunities for things to go sideways. Prepare for the crisis before it hits.
Water is going to inundate your low points some time during construction whether you like it or not. Plan for the event before it happens.
4. Drop Offs & Hazards
Safety in the construction industry is always front-and-center. It always seems like we never do enough, try as we might.
Today, while searching for drainage structures in murky water, I fell victim to a pavement drop-off. I was fine. Wet clothes. Slightly bruised ego. No big deal. We did have a manhole roundway that had become uncovered, likely from the surge backing up and forcing the plywood cover off the opening. Here are a few things to look for:
–Open holes need cover plates & ballast to hold them down, particularly in low points where pipe surge & backups might occur. A piece of plywood doesn’t cut it, it’s got to be heavy.
–Low point structures need to be marked-out somewhere visible. Paint marks on a wall (you can see my fresh, pink paint on the barrier wall, marking the 3 existing catch basins that we couldn’t find yesterday). When the area floods, anything on the ground is useless. Get your marks up.
–Mark out your drop-offs & hazards in your low points. You can see what we had in the picture (above) – Under water, you can see how it was easy for me go ass-over-tea kettle. This is a subtle Lessons Learned. I went swimming because I couldn’t see. Something vertical that you can see in a flood is all you need.
5. Milled HMA Surfaces WILL Blow Up in a Rainstorm
This issue didn’t befall our job, but it sure jumped out at me on the way back to the office: A neighboring project got hammered with the same weather. Halsted Street, which was milled on Monday by a City of Chicago contractor, looked like a Civil War reenactment site complete with cannonball craters and chuck-holes that could eat a car tire.
Look: Rain and milled HMA surfaces are not friends. They hate each other. If you mill a road and leave it open, you better damn sure be ready to make emergency repairs because, inevitably, your pavement substrate is going to be exposed and will get beat to hell.
6. Clean & Maintain the Erosion Control Systems
If you work for the Illinois DOT, then you know about Form BC2259 – Erosion Control Inspection Report. I’d say, in 9 out of 10 of our reports, one of the inspection comments always deals with the need to clean out inlet filters. I’ve never-much considered debris in the filters to be a significant issue. It’s an easy maintenance item, a no-brainer.
I was so pissed off – Our inlet filters were chock full of debris. Not just one or two, they ALL SEEMED TO BE FULL!!! And here I am with the contractor’s laborers, on our hands & knees in dirty stormwater pulling stuffed, water-laden silt bags out of catch basins! Now granted, Mother Nature unleashed on us and there was overland flow coming from all directions, so I get it, She smacked us in the back of the head pretty hard. But let me tell you something: Your frame of reference changes dramatically when it’s YOU pulling out half-packed inlet filters and not simply watching the contractor’s guys do it! So today, I had every right to be honked-off. Nonetheless, I don’t think I’m going to be the most popular guy on the site when our erosion report comes out and requires that EVERY SINGLE INLET FILTER ON OUR JOB BE INSPECTED AND CLEANED AS NECESSARY!
Do yourself a favor: Run through your job tomorrow and think about flooding. Think about backups. Think about scour and runoff and how protected you are. Don’t just fumble around the job filling out a report form because it’s on your checklist of things to do. Look ahead, plan for the crisis and work towards preventing it. Silt & debris are the enemy, so stay vigilant and do your best to keep your site in good working order.
7. Mechanical Systems Need to be on Readily Available
Our Contractor was not prepared for today. The scramble for a trash pump was simply that: A scramble. You need to make sure that you have the capacity to overcome a problem when gravity and fluid dynamics aren’t working together.
This is one of those deals where I get grief from a Contractor, about worrying too much. You know what: Worrying comes from experience. I’m not cocky by any stretch – In 30+ years of working in this industry, you develop a sense about what can happen. I’ve seen charlatans come and go. Guys who tell you “Aw, c’mon Bob, that’s not gonna happen, you worry too much, we can handle it if it does…” always make me nervous. While they might have good intentions and just want to allay your worries, they are just making excuses for not wanting to get themselves ready for battle.
We needed a pump. The Contractor didn’t have one readily available. The Kiss of Death. We were fortunate to have gotten help from our neighbor. An equipment company had pumps in-route, but our reaction time should have been better – This is an expressway, not a sidestreet. Don’t be afraid to ask your Contractor: Are you ready for “X”? If we get a “Y” out here, do you have what you need to fix it? Simple questions, hopefully, you get the right answers.
The Contractor now has a 4″ pump, hose & fuel stored in the Conex box adjacent to the area, so we are ready to go if the need arises again. We will use a protocol that if we are foretasted to have 1+” of precipitation, we’ll have our guys on standby in case things go sideways again. Everyday is a day to improve.
8. Plan More
Here’s my Impact Statement of the Day: As Construction Engineers, we don’t do enough planning or training. We don’t plan for crises or emergencies. We solve problems as they come to us, we don’t spend enough time trying to solve problems BEFORE they happen.
I was pissed at myself today: How did I not look ahead to this event? In this location? Why wasn’t I ready to react with good, solid, accurate information that could be implemented?
Why did I spend time looking for drainage structures that didn’t have active outfalls? Why didn’t I immediately identify where active existing structures were? It took me too long (in my humble opinion…) to develop the plan of attack. Yes, I was able to identify our strategy – But why didn’t I ALREADY have that strategy mapped out?
The worst part was that I did have it mapped out – It was in my truck!! I carry my battle map of this entire area, which I built to show the construction phasing with both the existing & proposed sewer systems on it – WHY THE HELL DIDN’T I REMEMBER THAT I HAD THIS???!!!
Here I am, ripping pages out of my plan set, trying to piece together 100-scale drawing together in a rainstorm. What the hell was wrong with me??!!
Again, that’s why this is a Lesson Learned article.
I need to plan more. Not plan more, like what tasks I need to get done tomorrow, or what route I’m going to take to my son’s baseball game Saturday. I’m talking sitting down and building scenarios. Building a crisis. Setting up time to train. Developing better battle plans for potential occurrences. I need to plan more. I need to prepare more.
What happens if we flood again? What happens if one of our overhead sign structures has an anchor come loose? Or if we encounter bad material while we’re excavating (that’s a topic for another article that hits close to home…)? Am I ready?
Look, we all want our jobs to go without a hitch, but we know they don’t. Prepare for problems. Develop crisis situations in your mind. What are your first 3 steps? How will you react? What will your communications look like? Do you have the information you need within arm’s reach to attack the problem? Spend a few minutes everyday training your mind and challenging your systems so you are better-prepared to react effectively when crisis hits.
And finally,
9. Be Personally Prepared
OK, so I’m going to let you in on a little personal secret that only my family and my nephew know: I’m one of those Prepper People…..
No, no, not the kind of doomsday psycho-people digging holes in their backyards or stockpiling 2 years worth of MRE’s and antibiotics. But, you can ask my wife and my kids and they will tell you: Dad is ready for anything.
I was pretty prepared today. My work truck is always Battle Ready. I have tools & towels & a Go-Bag filled with as many necessities & “Get Home” items that I can carry. But, even today, I didn’t have everything that I needed….
So, Lesson Learned about having the right “stuff” on hand would include things like:
-
A Complete Set of Dry Clothes & Work Boots
I got soaked from my ass to my toes – No big deal, but the drive home was a cold & clammy one, and it wouldn’t have been like that if I have thrown my change of clothes in my truck this morning. When you’re battling in the weather, you just have to suck it up and get it done – Comfortable being uncomfortable. But, it sure would have been nice to strip down and drive home with dry feet….
-
Backup Comms setup
My phone got wet – done. Fail. I lost my communication with Shearrisa, our IDOT RE, who of course, had comms up the chain of command. She couldn’t tell what was going on at the point of attack and I couldn’t communicate with her on our status in the field. Make sure you think through how you are going to communicate, how you will address power/battery issues, and what you’ll do if you completely lose comms.
-
Access to Pictures
I knew, in the location we were in, hunting for un-seeable manholes, that I had taken pictures. If I wasn’t having comms problems, I planned on calling Johnny back in our office to pull-up and text me progress pictures of the area we were working in. Note to self: You can NEVER have enough pictures. Digital is free.
Summary
Nobody got hurt today. There was no property damage. We did not have any stalled vehicles. Traffic was a crawl on the ramp and people got to their destinations later than they wanted to. We were one of dozens of roadway sections that got flooded out. It was a freak storm that hit the entire city. My clothes got soaked and my crotch was chaffed. All-in-all, this was a problem that got solved.
I look at today’s events as a test for me, our job, our crew & our Contractor. I’ll give us a B-. We did some good things. We battled the elements and the conditions hard. We got some great support from our neighbors. We developed a solution in some really lousy conditions and achieved some level of mission success.
But…
We were slow to the attack. We had the brain-power, but we didn’t engage quick enough. We didn’t have 100% of the knowledge that we needed to execute expeditiously. And we didn’t have the proper equipment and weren’t prepared like we should have been.
You can go back and read some of my old articles and find a common theme: You have to prepare. Don’t be a mouth-breather. Find ways to engage your mind into scenarios that, maybe on the surface seem completely ridiculous, but that will drive you to look at your site differently. Doomsday looks different to different people. Create the scenario and think through it. Have a sense of where trouble lies and how you will execute under pressure. Play in your imaginary sand table and develop solutions before the problem starts.
Discipline yourself to be ready to lead when called upon. I got a B- today. That won’t happen again.
Great article Bob!
Good article! There is magic in deciding how far down the preparation hole to go!