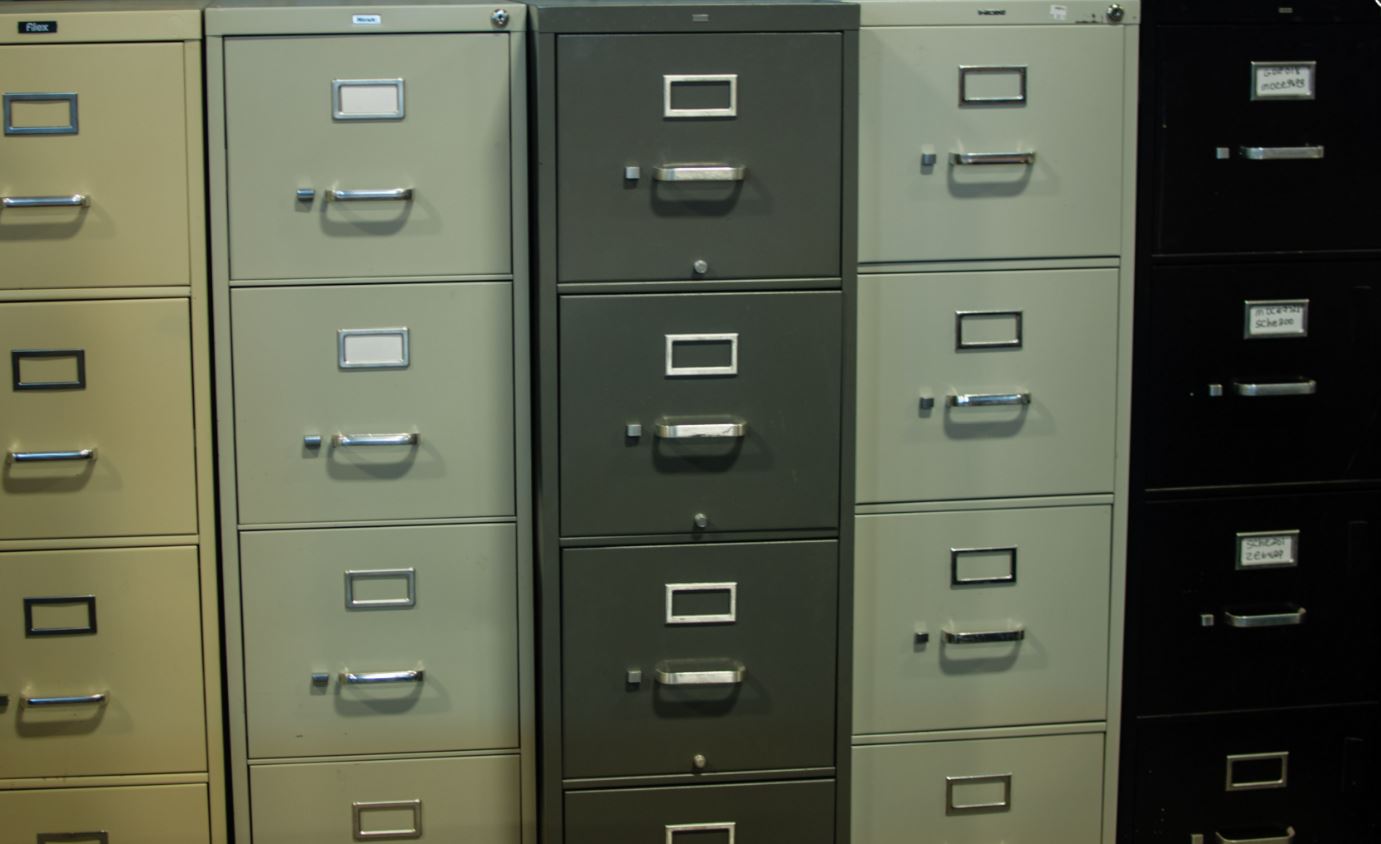
Well, if I was to assume that you survived reading my last article on Pre-Job Administrative tasks (CLICK HERE TO READ IT), you may have already had to hit the medicine cabinet for some Visene & Advil – It’s not a very glamorous subject by any stretch….
I would be doing a disservice to the crew if I just jumped-off from last week’s article and didn’t see the subject through.
There are still a lot of To Do’s to cover insofar as getting the necessary systems for new construction project fired up. In the last article, I covered many of the systematic-type items that we need to have established at start-up: Filing systems, letter templates, documents & contact information.
In this article, I want to get a little deeper into the weeds and look at some more-specific information that we need to have on-hand before construction gets going.
1. Begin With The End In Mind
One of the ways that you can start to think about the kinds of documents & pieces of information you need as the job progresses is to start at the end of the job and work backwards.
What do I mean?
Here’s a simple question to ask yourself: What does our crew need to turn into the client at the end of the job?
OK, I lied. It’s not a simple question….
Let’s face it: Soon you are going to be managing & navigating hundreds of documents. Dozens of issues. Hundreds of emails. You will be collecting documentation from your field crew about quantities, inspections they performed, issues that they resolved, field changes that they’ve made.
How are you going to keep track of it?
And worse yet: How are you going to find what you need when it is time to close-out the project?
Here’s the deal: You need to understand what documentation & information the client requires you to have in order to close out the contract. Once you know what your targets are, you can start to work backwards and dovetail your systems so that the information is readily accessible when you need it.
So, start looking at your client’s close-out requirements. What forms need to be filled out? What information is on those forms? How will you compile that information on a progress basis so that you have it readily available at the end of the project?
Start figuring out how you want to compile it now.
Let me give you a quick example – Pavement depth checks.
Let’s say you are working on a typical Illinois DOT project. The contract requires that certain types of installations (like concrete pavement, or topsoil or sidewalk) require the field engineer to measure & record the installed depth. That’s an easy task for the field engineers: Measure the depth, write it down in the field book. Done. Easy.
Here’s the problem: It’s now January, the field engineers have been moved off the job & you are in the field office trying to close out the books. You have 17 pay items that require depth checks and (because you didn’t do your due diligence like I suggested….) you just now find a close-out checklist that YOU have to complete that contains this item:
Holy “Where-the-Hell-Are-All-the-Depth-Checks” Batman?? Good luck having to go back through 23 field books trying to verify that we have the proper documentation. Damn, if I had just been keeping a log somewhere….
You see the issue, right? Get ahead of it now. Establish your system(s) to keep track of the important stuff. Believe me, your job close-out work will be much easier if you do.
Let me give you a tickler list of some of the items to consider:
–Final forms & close-out checklists – Review them now and figure out what you’ll need at close-out
–Shop drawings / Operations manuals – What needs to be given to the client?
–As-built drawings – Are you keeping a current set somewhere, with all of the revisions included in it? Where are you keeping your red-lines that you need to incorporate?
–Pay items that require thickness cores, surface variation tests (bump tests, profilograph, etc.)
–Vertical clearance measurements – These can be interim measurements during construction, especially if you are resurfacing under bridges or sign structures
–Structural testing reports (such as ROCAPS for bolt testing, pile driving, caissons)
–Paving reports (HMA, PCC, bridge decks)
All the items on this list are very common to road & bridge projects, but you can expand/contract the list as your project & client require. The key is to do your due diligence now and start setting up your systems so that, 8 months from now, retrieval of the information will be a snap. It can be as easy as designating a file called “Final Papers” where you keep a copy of the day-to-day pieces of information that you’ll need in-hand at close-out. The more you start looking ahead, the better prepared you will be to have the proper documentation assembled when you need it.
2. Develop a List of Start Up Forms
Most clients don’t allow a contractor to start construction without having lots of pre-approval documents in-hand. Go through your documents & find out what information is necessary.
I know that I’m pulling my sources again from the Illinois DOT, but they have numerous documents & tasks that need to be completed before a contractor starts work that are pretty common to any type of construction project.
Here’s a list of Leading Questions to get you thinking:
–Have you submitted the proper Construction Start reports to the client / agency?
–Have the Communication Center or other EMS agencies been notified of the project’s start? Who else needs to know we’re going to start the job…?
–Do you have to mobilize changeable message signage with public notification messages, or other static advance notice advisory signage?
–Does the agency need to issue a press release about the job starting?
–Do you have all of the necessary approvals & permits in-hand to start work?
These are just examples, and your client may have more or less for you to do. The key is knowing what is required & getting the tasks & information required done.
3. Permits
Permits are a way of life. There’s little to no getting around them. Government agencies live for permits. They are a necessary evil.
Before your job starts, assemble your permit list.
Here’s a tip: Never assume that all the permits are secured. Until you see them, they aren’t approved. Remember, YOU are in-charge, YOU need to have a handle on the approvals. Get engaged with the process.
–Village utility permits (sewer, water)
–Electrical
–Stormwater
–Environmental
–Natural Resources / Army Corps / Floodway
–FAA (if you are near airport facilities)
–Railroads
–Traffic Management / Lane Closures
4. Progress / Routine Reporting
Ah, progress reports. Paperwork. More forms to fill out….
Reports need to get done: It’s that simple. Develop your who / what / when’s early in the job set-up so that everyone on the crew knows who will be responsible for what.
There’s a quick list of typical reports that a construction staff will produce:
–Daily Job Diary Entries
–Daily Staff Activity Reports (manhour, vehicle, fuel & expense charges)
–Weekly Resident Engineer Reports
–Weekly Traffic Control Inspection Reports
–Weekly Erosion Control Inspection Reports
–Roadway Lighting / Traffic Signal Ops Inspection Reports
–DBE / Trainee / Labor Utilization / Payroll Reports (typically generated by the contractor)
–Progress pictures / videos
Vince Cirrintano, who was our crew’s IDOT Resident Engineer during construction of the Arsenal Road Interchange project in Will County, Illinois, was a stickler about us getting the job’s weekly report to him on Monday morning. Now, you could say, “Aw, c’mon, what’s the big deal if I don’t get it done until Tuesday? Really? I have a busy Monday today and I don’t know if I’ll be able to get to it…”
I’ll let you in on a secret: Establishing routines for you & your crew are THE #1 way of making sure you are getting your paperwork done. I learned this by Vince setting the standard. It is one of those lessons that will stay with me long after I retire.
We ALWAYS got our RE Weekly reports to Vince on Monday. I honestly don’t think we ever missed. As the client, he never had to worry about us NOT getting our reports in.
Set-up the same type of Standard Operating Procedures with your inspectors for traffic & erosion control inspections. Set the day that YOU want them in your in-basket. No, you’re not being an asshole by setting standards for your crew to stick to – YOU set the bar.
All of this information needs to be systematized. Plan the work then work the plan. As the leader that’s your job. Get it straight.
5. Materials Tracking
Dealing with material approvals can be a royal pain in the ass. That is true, of course, if you are unorganized and don’t have a system in-place to manage them. There will be a boat-load of information making its way through your field office. Know how you & your crew are going to manage it.
Concrete + HMA + Aggregate + Rebar + All the Other Materials = Lots & Lots & Lots of tickets…..
Prepare for battle now. Get your files & logging system setup pronto.
If you are lucky enough to be able to delegate this task to someone on your crew (like a documentation engineer or a materials coordinator) I’m going to make a suggestion: Get Involved!!
Here’s something that bites first-time Resident Engineers in the ass: “Oh, I just let ____ (fill the duly-appointed person’s name in the blank) take care of all the materials stuff. It’s really confusing and ____ knows what to do so that means that I don’t need to be directly involved.”
Don’t say it.
Listen: Duplicity at the task level is mandatory. It’s a weak position on your part to shlepp 100% of the front line responsibility off to subordinates because you don’t want to get involved. That’s lazy leadership on your part. Don’t be that RE. YOU need to understand the process. YOU need to be able to take over the reigns if something on your job goes sideways. As the leader, there is NO TASK that is below your command. Take ownership.
The materials logging & tracking processes, especially for government agencies, can be quite arduous. Getting all of the submittals, tickets, off-site inspection approvals, etc. completed is a huge part of any RE crew’s duties. You need to establish a system within your crew that is efficient & effective. Having multiple people, including yourself, who are well-versed & active in tracking & monitoring the documentation only strengthens your team.
Getting concrete tickets logged-in? That’s an easy task. Logging & tracking all of the test results, off-site approval, QA/QC-type documentation? Now that’s a chore! It’s your job to make sure that the paper is flowing properly.
Here’s my advice: Stay active. Keep yourself engaged with the process. Ask questions of the people who are assigned to keep track of this information. Have systems in-place that allow for multiple crew members to know & understand how the documents are to be managed, filed, logged & monitored.
6. Review Client / Agency Checklists, Specifications & Forms
It’s hard for me to write this section as a generic, one-size-fits-all paragraph since we all work for different clients (public & private) or government agencies that each have different requirements. But, just so we can frame this topic, let’s focus on work elements that we all typically get involved with, like pavements, structures, lighting & utilities.
Here’s my tip: Seek out as many agency resources as you can OTHER THAN THE ONE YOU ARE WORKING FOR and try to adapt it to your management system.
What do I mean?
The majority of projects that I’ve worked on deal with transportation facilities. For the most part, the Resident Engineer has similar functions & responsibilities no matter who the agency is. Take advantage of all of the documents that the “other” agencies have published and apply them as you can.
IDOT publishes checklists, manuals & guide books on virtually every conceivable roadway installation possible. Grab them. Print them. Read them. Apply them to your project.
Don’t be afraid to challenge yourself to find some other, alternate resources. Just because I’m building a project for the Illinois DOT doesn’t mean that I can’t seek out inspection methods in, say, Iowa, right? Although each state might have it’s own requirements, it doesn’t mean that you can’t apply something that they do to how you carry out your duties.
Expand your knowledge base. Find out how other agencies operate. Apply the nuances that you like to your own work.
And when is the best time to review a construction checklist? My answer: ANYTIME!!!
I can hear you now: “Bob, I’m not going to be installing any sewer for months. We’ve got traffic staging coming up, we’ll have to get the existing pavements removed. I’ll look at the construction inspector’s checklists later….”
My ears are turning red just reading that..!!! You won’t be working on my crew if that’s how you think…
Do you want a motivator? Ask yourself this question: How much time have you wasted in the last month hunched over your phone? Be honest with yourself. Could you have used some of that time to increase your knowledge base? To plan for this construction season’s work? Have you extended your skill set? Or have you pissed away those hours on YouTube and FaceBook…..?
You don’t have to answer that. Plead the 5th. I try not to ask questions that I don’t already know the answer to….
Look – YOU need to get this job setup NOW! Not in 2 months. You need to be looking ahead. You need to be thinking about the work that won’t occur for months. Start planning. Review. Prepare. Train.
Reviewing checklists, or construction forms that you’ll be using gets you thinking ahead. You will spawn new ideas in your own head during your review. You don’t have to do a detailed read of all of these forms, just scan them & look for “paperwork-type” issues that you need to navigate.
It bears repeating: Get yourself ready NOW.
Close-out
If you can get all of these documentation systems set-up and ready to go before the contractor breaks ground, you will be well-ahead of the proverbial curb. I sound like a broken record, but that’s said from experience: Strive to get your paperwork systems established as soon as you can. Cold weather months prior to construction give you a huge opportunity to prepare. Believe me, it will be a load off of your mind allowing you to concentrate on managing the project (not worrying about paperwork systems….).
My next (and final….) article on pre-job setup will have us heading out to the field to get all of our pre-construction documentation done. Once we get our existing conditions documented, we’ll be as ready as we can be for the construction season to commence.
Be the first to comment