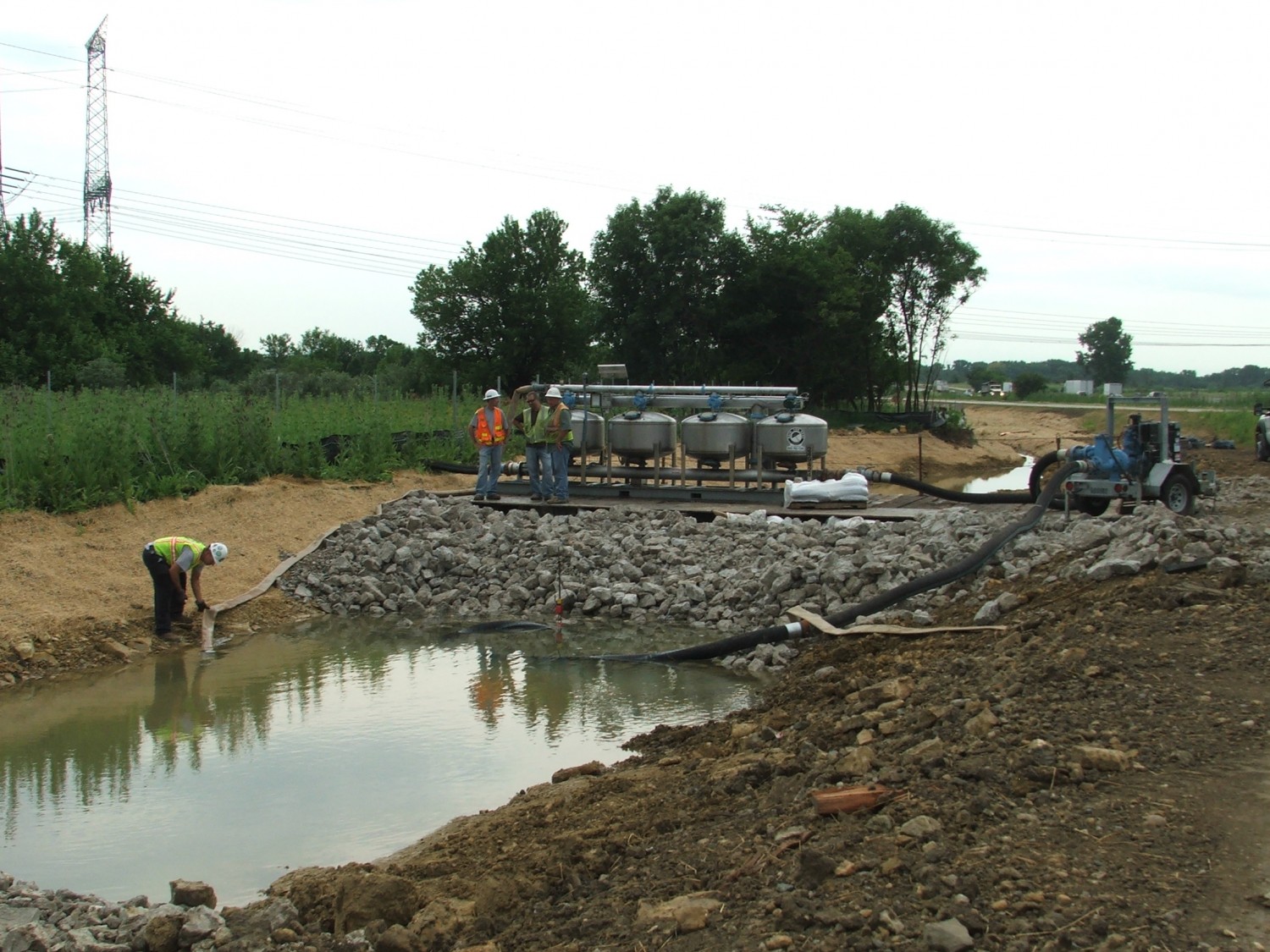
So in my previous post regarding on-site stormwater treatment challenges (CLICK HERE), I described the unsuccessful treatment strategy we implemented on our Arsenal Road Interchange project using a stormwater filtration system. It was a great idea and was implemented as we wanted, but it simply didn’t work for the particulate matter that we were trying to remove.
Why Didn’t It Work
So here’s what we found out through the course of testing the system through several storm events.
Unstabilized Tributary Area Was Huge
The interchange construction area was massive. One of my flow rate calculations (used to size the filtration system) showed that just the east side of the interchange had a tributary area of over 112 acres, which included both the exposed rock detention basins as well as an adjacent wetland. The pumping system could only manage 900 GPM, so it forced much of the runoff to be held within the detention areas. That was a good thing, however…
The detention basins were cut from rock. Any precipitation we received flushed the exposed rock, essentially washing the silt & dust from the rock breaking activities into the detention areas. Since there was no final stabilization for the ponds (the finished surface was going to be rock, & you can’t get grass to grow on exposed rock….), the flushing could not be prevented.
Storm Events Were Frequent & Heavy
Summer, 2011 was a very wet period. Several 1.5″+ rainfall events occurred on a much-more frequent basis than the historical data could have anticipated. Ma Nature decided to punch us when we didn’t need her to….
Sediment Basin Was of Little Functional Use During a Storm Event
The combination of large detention basin and frequent, heavy rainfall events taxed the settlement abilities of both our detention & settling basins. While our settling basin adjacent to the filtration system did allow for some settling during low flow periods, it served virtually no use during large storm surges since it was being volumetrically overwhelmed.
Filtration Media Was Ineffective
The use of the filtration system, on paper, was thought to have the potential to mitigate our condition. Unfortunately, we learned through trial & error that the sand filtration media just wasn’t providing enough sediment removal to satisfy our needs. We were using an extremely fine sand media, but it wasn’t fine enough to clean the silts & clays in suspension.
So How Clean Is Clean?
In 2011, the NPDES permit requirements for sites that disturbed more than 20 acres required that the stormwater discharge was limited to 280 NTU’s. I believe that in Illinois, the 280 NTU threshold is still the requirement for construction site discharges.
Hold on: What’s an NTU, you ask? Let’s dig into the weeds a bit…
We discussed earlier the condition of Turbidity, which is when water is mixed with sediment, such as our case when precipitation is agitated with silt, clay & rock fragment dust. The particles are now in suspension since they do not have enough mass to settle.
The scientific means of assessing water quality insofar as suspended solids is concerned uses Nephelometric Turbidity Units (NTU’s). It’s a fancy measuring system for gauging how cloudy water containing suspended solids is.
Bottom line: The sand media in the filtration units could not achieve discharge at < 280 NTU’s. Compare the picture below to the water samples in the NTU description: You can see it, just like we did: The particles in suspension where just too fine to be removed mechanically.
So, we had to go back to the drawing board to find another solution. And as if the swimming pool filter idea was far fetched, you won’t believe where we found the next idea…..
Magic Through the Food Industry
So let me blow the dust off of my circa-1984 Michigan State University issued edition of Basic’s in Environmental Engineering for a moment and refresh a concept that we all learned about way back when that deals with flushing the toilet.
Let’s talk about flocculants.
Recall that when we flush the toilet and our byproducts end up at your local municipal wastewater treatment plant, where a magical transformation of our output occurs turning the wastewater from dirty to clean.
Let’s review our environmental engineering books, just for a second.
Waste products get sent to the local waste treatment plant. Our effluent is initially screened to get the non-biological stuff filtered out, like rags, plastic and other non-biodegradable stuff. A flocculent is then mixed in with the effluent. Flocculants, in the case of wastewater treatment, are naturally occurring “bugs” that eat the goodies we’ve flushed. As those bugs eat, quickly grow & subsequently die, they gain weight and “fall out” of suspension because they are too heavy to continue to float. The particles sink to bottom of the settling basin leaving clean water above the settled sludge. The water is pumped off, processed and returned back to Mother Nature for more natural handling while the sludge is collected, processed, and reused as fertilizer or other bio-related products.
So how could this process be used with muddy stormwater runoff? You guessed it: Flocculants. And get this: You’ve probably eaten some of the flocculants we used in the past few days….
The food industry uses polymer-type additives to lots of food that we eat in order to coalesce food particles. Think about gummy bears. Or Smuckers jelly. Or spaghetti. Lots of different types of starches & proteins are added to food to provide density to liquid-based ingredients, basically using chemical properties to bind food particles together.
So, we discovered that there were several manufacturers that used similar food-based polymers to develop technologies, applying the theory of binding food particles together with additives, and use them for environmental clean-up efforts.
So What the Hell is a Floc Log?
We ended up being introduced to a product line developed by Applied Polymer Systems called Floc Logs (CLICK HERE FOR THEIR WEBSITE). These blue, gelatinous bricks were made from polymers that were similar to those used in the food industry. The idea was to expose the sediment-laden effluent to the Floc Logs, agitate the mixture and then release it through a sediment channel where the particles would coalesce and “fall-out” similar to the waste treatment plant example we looked at. And because the components are food-based, they could be released into natural environments without cause for harming plants, fish or wildlife.
Now wait a minute: You mean to tell me that if I put some big, giant blue block of jelly in some cloudy, murky water that, after churning it up a little and letting it flow through a ditch that the water would be clean by the time it got to the creek? No way….
Way.
And if I hadn’t seen it with my own eyes, I’d have never believed it. It worked. Oh man, did it work!
How We Used Floc Logs
We, discouragingly, had to remove the filtration system, since it did not work as anticipated. But using the same settling basin, we pumped the effluent over the Floc Logs and allowed it to be in contact with effluent. It was basically like spraying a hose on a bar of soap. But at this stage, the stormwater had been exposed to the Floc Logs.
You’ll see in the detail below how the “ditch system” was to be setup.
- The floc-laden effluent flowed over a burlap / jute mat-lined ditch. This is where the majority of the “fall-out” occurred
- A rock-lined sump ditch check was provided prior to the ditch’s discharge, providing an additional area where “fall-out” occurred.
And at the end of this ditch system, clean water appears.
Here’s what it looked like in action:
It is absolutely amazing technology.
The overall cost of the Floc Log solution was another great feature of implementing their use. Each log cost about $75, and there was labor & equipment costs to remove the silted jute/burlap ditch lining. But compared to the ≈$75K that the filtration system cost to install, operate, maintain & remove, the cost of the Floc Log system was an order of magnitude cheaper.
I kid you not: It was like magic, I swear to God. We had been struggling with this issue and had little success despite implementing as many BMP solutions as we could think of. When we saw the Floc Logs working, guys on our crew were in a state of disbelief. It turned out to be an amazing success story.
Sediment Treatment After Arsenal Road
Subsequent to our success with the Floc Log system success at Arsenal Road, we implemented the solution again at our Illinois 19 / York Road project in Bensenville, Illinois, where we managed site-generated effluent using a portable sediment baffled container, combined in series with the Floc Log / jute-lined ditch setup. The results were equally successful: The pre-treated effluents dropped the heavy materials in the siltation box and the fine particles were removed in the ditch. 2 for 2 – We were batting 1.000. Well, the Flog Logs were batting 1.000, we just happened to be supplying the bats….
There is no doubt in my mind that, as more and more engineers are exposed to the flocculent technology and its uses in stormwater treatment, Floc Logs and polymer-based solutions like it, will become a staple BMP just like silt fence and ditch checks are today. I do not know how the specifying community is implementing these types of solutions into current erosion control design schemes, but I am hopeful that we get to the point where polymers are routinely specified in our construction documents. I’ll continue to recommend their use on any of our projects. Seeing is believing.
I’d be happy to provide you with more information & system set-up specifics as we applied them. I’m certainly not as versed as the guys at Applied Polymer Systems, but I can certainly assist you with getting started implementing the technology. Reach out to me and I’ll be happy to lend you a hand.
Be the first to comment