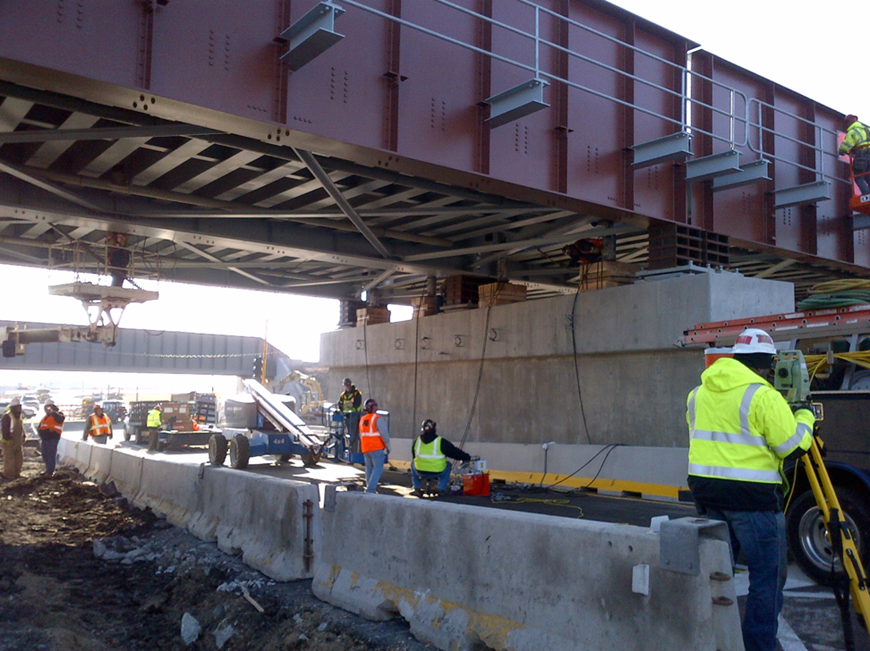
I can remember it like it was yesterday.
1992. The Kennedy Expressway. The inbound lanes between Logan Boulevard & Fullerton Avenue.
George Bartishell was Consoer, Townsend & Associates survey crew chief where I worked. We were in the field office and George came up to my desk.
“Hey Bob, have you done any surveying before?”
“A little bit, but not much” I told him.
“Good. Get your boots on & come on with Dave & I” George said.
Dave Miketinas was another surveyor on our crew. The 3 of us headed out to the Kennedy Expressway to layout pavement. I had never done anything like layout before, but it was time for this 20-something young, energetic civil engineer to be baptized.
Little did I know that the skills that I learned working with George & Dave would be the start of an entire section of my resume.
I have spent a good portion of my construction & engineering crew behind a survey instrument. I have run my own survey crews. I have done tons of level work. I laid out an entire strip mall complex by myself with a robotic total station.
It is a tough living. It’s not just physically taxing on your body, but it is even tougher on your mind.
The stress that surveyors & construction layout technicians have to deal with on a daily basis can be excruciating.
You have to be right. All the time. You can’t miss. Your layout needs to be accurate sometimes to the 0.01 ft in 3 dimensions. The guys building the projects from your layout expect you to be precise. And they want the layout 2 hours ago….
It is not a job for the faint-at-heart.
I’ve lived the life of a survey crew chief. While I loved the physical nature of the work, the ability to look at a site and actually see my or our crew’s work living as lath & flagging & hubs, PK nails & cross-cuts, I did not enjoy the pressure. The pressure of having to be right every single time is a lot to bear.
But, that is the life of a surveyor.
Here’s my Statement of the Day:
The construction layout crew has the toughest, most-stressful job on the site.
You can debate me and tell me that tradesmen have a tougher job. You can argue that the physical demands of a 12-hour day of hard, hand-on labor are tough. And to some extent, I agree. But I’ll tell you this much: I’d much rather be behind the controls of a Bobcat, or in the bottom of a trench setting storm sewer – Why? Because at the end of the day, sure you’re dirty & beaten, but the day is over, the job stays behind until tomorrow. But, when you you are a surveyor, not only did you physically grind all day, you’re mind is ALWAYS on the job….
I wanted to start this article by laying some groundwork for this post-mortem look at construction layout. I needed you, the reader, to be able to capture the weight of what surveyors on construction projects feel. When things are going right, layout is a ton of fun and a great way to earn a living. But when things go sideways, or when stuff is laid out in the wrong place, sleepless nights are born.
I wanted to share the story of one of those sleepless nights. I slept OK that night, but I don’t know if Larry did….
Let’s Head Back Bensenville, Illinois
In a couple of previous articles, I chronicled some of our crew’s goings-on in Bensenville, Illinois where we were involved with constructing a 2-track railroad bridge for the Canadian Pacific Railroad. All-in-all, it was a good job to work on. I think that everyone involved with the project was happy at the results despite the bumps-in-the-road that every project experiences.
For the most-part, the structure was not very complex. Although we had challenges with much of the abutment piling, erection & installation of the structural steel went without a hitch.
The Center Pier
In addition to the abutments, we needed to construct a center pier. The work zone was pretty tight: We shifted traffic on either side of the pier. Irving Park Road’s vertical profile would ultimately be lowered by about 3 feet from where initially was, so the excavation for the piling & footing created a pretty deep excavation that required shoring.
Despite the tight access to the work area for equipment & materials, getting the soldier piles & lagging was time-consuming, but the Contractor got the excavation completed. The next step: Piling.
Meet Larry
I first met Larry Harvey, the Contractor’s surveyor, I had already heard great things about him from the Contractor’s project manager. He had raved about Larry’s work, how conscientious he was about his layout, and how he had circumvented numerous problems on the last project they worked on together. Larry was a keeper, which was the reason why he was on our project.
So first impressions are lasting ones. When I met Larry on the site, he was in full layout mode: Survey pouches on, backwards hardhat with a railroader’s bandana on head. It was 0730 hrs and he was already in a flop sweat. A hard working guy by every stretch. I could tell in a couple minutes that Larry was Good-to-Go.
Construction Layout on a DOT Project
In this article’s opening story, I told a quick story about the Kennedy Expressway. That was back in 1992, and at that time, the layout of the construction work fell on the hands of the Resident Engineer and his crew. As time passed, agencies started shifting the responsibility of physically laying out the job onto the Contractors, leaving the Resident to be responsible for just checking the Contractor’s layout.
I have always had mixed emotions about this. While the shift in responsibility ultimately brought with it a shift in the respective liability from the Resident to the Contractor, it took away a front-line diligence of the Resident needing to have a solid grasp on how the job was fitting together. When you do the layout, you know where things are, and you are in a position of being the “First Responder” to problems. “Checking” layout is much different than “Providing” layout.
Layout requires a three-pronged attack:
1. Calculate the points that need to be laid-out
2. Physically layout the points
3. Re-check, or cross-check, or have someone else check your layout to see that it works
In government construction contracts, the Contractor performs #1 & #2. He also (if he’s good & conscientious…) will do #3 himself, but the Resident Engineer’s crew should also perform #3 to confirm that the layout is in the right ballpark.
You may be surprised to hear me say this:
I think the hardest construction staking task is not physically laying out the points, it’s calculating the points.
Calculating layout points is time consuming. It is often-times done by the surveyor by hand on his lap in the front seat of his truck. It is sometimes done by a person in the surveyor’s home office who is calculating & developing the point files for the survey crew to layout. It takes time. And it has to be right.
Often times, the surveyor is put under duress. Time is of the essence. Equipment & labor forces need layout to work. Idle time waiting for layout costs everyone time & money. The surveyor might be in his truck, using a calculator & a magnifying glass, trying to read reduced-sized copies of the prints. The clock is ticking. Money is being spent. And the surveyor holds a lot of cards from the deck.
Pulling points is stressful. Being the guy in-charge of layout is stressful. Working under duress is stressful. Bottom Line: Construction staking is stressful.
Back to the Center Pier
After the Contractor finished with the excavation, Larry laid out the offset marks for the pier’s footing & piling lines. Our survey crew came behind Larry and shot his marks. Just another day at the office.
That afternoon, our surveyor, Dave, swings into the office. He explains that, well, something isn’t checking. He ran his numbers in his truck by hand and wondered if I could jump onto Microstation and see if I could pull some lines & offsets as a check.
I remember spending a couple hours working with the electronic files. I remember having to do some correlation work between the bridge plans & the roadway plans. The designer had often switched railroad & roadway alignments when detailing design points, so there were occasional encumbrances that this back-and-forth caused.
When it was all said-and-done, I plotted what I believed to be the layout offsets for the pier’s footing. And what I found had me rattled.
I told Dave, our surveyor, that I was missing Larry’s points by, like, 11″. That never happens, Larry is ALWAYS spot-on. And Dave was getting the same numbers: 0.88′ to the west.
Now I’ll give you a little secret into the way my brain works: When something is wrong, I almost always assume that I’m the one who’s wrong. Catholic guilt? Anal retention? Some sort of psychosis? I wish I knew what makes that happen….
I thought I must have something wrong. But, that would mean that Dave’s shots would have been wrong too?
I stayed in the office for a couple extra hours that night, re-running the numbers.
The next morning, Dave was on vacation and Joe, one of our other surveyors was on site. I gave Joe the scoop and asked him to check the points, but setup on a different control point, that way we could see if we had a problem with our control.
About 2 hours later I got a call from Joe: Yup, same answer. He was hitting Dave’s numbers the same.
I can’t find it. Something’s not adding up.
I called the Contractor’s project manager and reported what we were finding. I told him that I would be totally happy if we were all wrong and that Larry had it right. But, if he could let Larry know, it might be good for him to do a double-check, then at least we could find where our bust was.
And oh, by the way, the Contractor was planning on starting pile driving tomorrow….
The Phone Call
There isn’t a surveyor in the world who wants to get “That Phone Call.” It’s the call that makes your heart palpitate.
As a surveyor, when you leave the site, after getting your layout points in, you are onto your next task. You aren’t looking backwards, you have too many other tasks to get to.
When the call comes in from the field reporting that something with the layout doesn’t seem right, your gut starts to twist.
What did I miss? Did my control point get disturbed? Instrument calibration? Did my rodman have the backsight set up correctly? Did I double check my offsets? How did I run my calcs? Did they build anything yet? Are the guys standing around waiting?
Breath in. Breath out.
I followed-up with an email to the Contractor’s PM. I had to formalize the potential issue. The next morning, he sent an email to Larry:
You don’t even need to actually be Larry to feel the gravity of that request….
So After Some Digging….
I got a phone call from Larry. I don’t remember if it was late Monday night or very early Tuesday morning. And I don’t really remember the exact details of what we discussed. What I remember was the outcome.
Larry and one of his engineers re-ran their numbers. They found the problem: When the layout points were pulled by the engineer in the office, they had a slight bust in the alignment that they used. Larry already had his new points calculated and he would be getting them re-laid out.
He got them laid out. We checked them. We were within 0.02 ft of each other. Pile driving could get underway.
Phew.
As much as I don’t recall the specifics of that phone call, I remember Larry thanking me. And it wasn’t the run-of-the-mill “Thank You” like you say to a clerk in a store to be polite. It was a heart-felt, from-the-pit-of-the-soul “Thank You.” That “Thank You” came with feeling. It was the kind of “Thank You” that, even now, many years later, I still remember and that I won’t forget.
Stepping back, anyone who hears this story can appreciate the outcome. A problem was averted. Nobody needed to be patted on the back, no parades with circus animals & marching bands. And nobody needed to be called-out, blamed for a problem, the job wasn’t going to spiral out of control. This was simply professional people working together to solve a problem. No strings attached. No egos to check. No arguments or accusations to be had. Problem. Solution. Solved.
Lessons Learned
This article has been one that I’ve wanted to write for a long time. It is a great example of collaborative effort on a construction project. It’s an example of what makes working as a construction engineer rewarding.
Let me run through some notables that we can all glean from this story:
1. Back Checks are Essential
Do you know why traffic signals have multiple lights? When one light is out, there are others that are working. That’s “duplicity” in action.
Construction layout depends on having more than one person, crew or entity involved. To depend on a single source of information is to run the risk of having that single source be wrong. And in construction, wrong means $$$.
Any good contractor & any good Resident Engineer appreciate the need for comparative checks of the work. Humans are imperfect creatures. Unfortunately, the contractual clause that lawyers write & expect us to follow don’t allow for anyone to be wrong, lest there be consequences. As construction engineers, our job is to do our best to eliminate & avoid things being wrong.
As an RE, you need to establish a high expectation for back checks. The Contractor’s layout needs to be checked. Sure, you could find the contract clauses that make the Contractor 100% responsible for his work. But here’s the real story: When things go sideways and work is installed in the wrong location, everyone near the fan gets sh%t sprayed on him.
It’s pretty rare when Contractor’s don’t want their work checked. Most guys appreciate the 2nd look at their layout.
Lesson #1: If you’re not implementing it already, make survey back-checks Standard Operating Procedure for your crew.
2. Demand that Control Points are Compared
When it comes to control points & benchmarks, one of my tenets is to ALWAYS run independent control point checks and compare them with the Contractor’s surveyor. NEVER assume the control points & benchmarks are 100% correct. Do you own control loops and check them for yourself.
It is inevitable that you find out that some of your control points & benchmarks don’t close when looped. Control points get hit. They get damaged. Utility companies tear them out on accident. There is time that passes between the time the job’s designer did his topo survey and when you started construction.
Your survey crew needs to run its own, independent control point checks. Then, you need to do an independent comparison with the Contractor’s surveyor’s measurements of common points.
Write this down: NEVER blindly “just give” your control point data to the Contractor. ALWAYS compare your data with him.
I’m gong to rant here for a minute…
My thoughts on not arbitrarily giving control point information out comes not from a point of being a jerk, it is simply to maintain data integrity. Contractor’s surveyors have gotten pissed at me for being “so selfish” with my/our data. Like, because I’m the Resident, I’m just supposed to give you my data for you to use, like I owe it to you. You know what: Tough Sh&t. Go ahead and call me an asshole, I don’t much care about you getting your feelings hurt.
I want to compare my data with the plan data. I want to compare the points with the Contractor’s data. I don’t want to assume that your data is right, and I don’t want you to just take my data and apply it. We always want to make sure that we are all working from a similar, comparable control point system. That is Duplicity in Action.
On my projects, I’ve made it a habit of running the cross-comparisons. This is “First Week on the Job” type work. These are easy checks. It validates duplicity between survey crews. It’s performed independently. It maintains the theory of checks & balances. You never have to worry about layout points not checking because of control point differences.
3. Drop Everything and Help Your Surveyors
By now you’ve picked-up on a theme in this article: Construction layout work is a pressure cooker. The layout crews are constantly under duress. They are pushed by the Contractor. They are pushed by their home offices. They have to hit the beach-head running and hit the nails on their heads EVERY TIME.
How can you help? Support the surveyors at all costs. Drop what you are doing and help them when they need it.
I am a rare breed: There aren’t a lot of construction engineers who have worked on both as management, technical engineers AND muddy-booted grunts. I have a unique perspective in being able to proficiently use Microstation, survey equipment AND still be a technical engineer & administrator. It is from that perspective that I understand how much goes into preparing a survey crew for layout work because I’ve already lived it.
While your acumen may not have the depth as mine, you need to be able to pool & use the resources that you have available to you to get issues resolved. When your surveyors need help, use all of your tools to jump into the foxhole and help them. When you can, apply your personal knowledge & efforts, do it. And when you are over your skis, get the questions answered. Don’t leave the survey crew to fend for themselves – Run towards the proverbial gunfire and help get the problem solved.
4. Don’t be the A-Hole Surveyor….
I have worked with some outstanding surveyors in my day. When your surveyors are getting the layout points in the right place on a consistent basis, it’s like a weight off your shoulders. Great survey crews will keep you and your project out of harm’s way more times than you will ever realize.
But, for every 100 great surveyors, there is at least one or two jerks. I’ve worked with them. Pardon my French (but you can handle it…): Straight-up, down-right classic assholes.
For whatever reason, surveyors with big egos can be very off-putting. Some guys don’t want their work checked. THEY ARE RIGHT. They are ALWAYS RIGHT. “Listen, Son, I’ve been doing this since the days of chains & railroad spikes, before you knew where Sesame Street was.” They are never wrong. They like to make you feel like you don’t know enough to question them. “So listen here, Lad, you just go back to your office and let me handle the layout, don’t you worry about it….”
There’s nothing worse than being stuck working with an egotistical surveyor. NOBODY likes to work with assholes, least of all, me. I’m getting too old, and I don’t have the patience anymore to deal with people like this. As a Resident, I just want to build the project right. I want you to get things in the right place. I’m not here to make you make you look like you don’t know what you are doing, or to challenge your abilities. I just want to help get it as right as we can. Our team is here to help if we can. Use our expertise to your advantage.
Running across guys like this in our industry is un-nerving. But you know what: They are out there. And I’ve learned how to deal with them: You know what, Pal, you’re on your own. I’ve got other tasks on this site to take care of. And oh, by the way: I hope you get everything in the right place today, and tomorrow, and for the next 2 years of this project because, well, if you miss, I’ll remind the Contractor’s PM about your not wanting us to check your points. PS: Have a nice day….
Nobody wants to work this way. I sure don’t. And in 30 years, I can count on one hand the guys like this that I’ve run into. But the lesson here: Be aware that guys like this exist. Deal with them straight-up. Be direct. Offer to help. If they take it, that’s great. And if not, it’s their problem, not yours.
And this leads to my last point:
5. Put Your Ego Aside
The reason I wanted to tell the story of Larry and this situation was because of the carry-over its theme has in so many spheres.
If you can put your own ego in check, listen to those around, and work towards a common solution, your world will be a lot more enjoyable.
Larry didn’t have an ego. Larry wasn’t upset when we asked him to double-check his numbers. Larry wanted everything right just like we wanted it right. Larry knew that we weren’t challenge his integrity. Or his skill set. Or his expertise. Larry appreciated us jumping in.
What if Larry was an asshole? Would I have responded differently to the problem?
Probably not. We’d have still run the numbers. I’d have still let the Contractor’s PM know there was a problem.
But, would I have gone the extra mile? Would I have forgone seeing one of my son’s baseball games so I could stay late in the office trying to help? What would you have done?
The story had a happy ending. I attribute that to a bunch of guys who had the right mindset just wanting to do a good job. Collaborative effort in action. Professionals doing what they do.
Close-Out
We all have to remind ourselves, now and again, that the surveyors have a very tough job. NEVER take them for granted. ALWAYS support them. Check them. Lend them a hand, both physically & technically. Offer to get in the field with them and to work with them. Learn the trade for yourself. Don’t be bashful. Ask to get behind the instrument. Get outside and pound stakes, scribble layout data on lathe. Learn how to layout line & grade. Expand your skills. Every day, strive to be a Full Service, Well-Rounded, Do-Whatever-It-Takes Engineer.
Bottom line: Make sure you have backchecking as part of your crew’s Standard Operating Procedures. All it takes is for you to find that one needle in the haystack and avert a problem. The time and effort you and your crew spend on it is ALWAYS worth it.
Be the first to comment