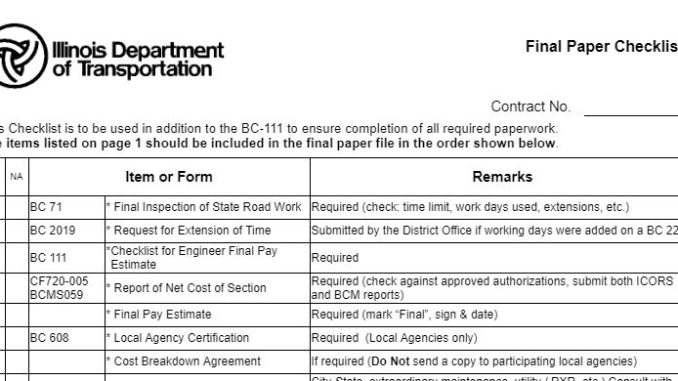
What’s the best time in the lifecycle of a construction project? The day that your boss tells you that you’ve got a new job assignment.
What’s the worst time in the lifecycle of a project? Closing out the job….
OK, well maybe it’s not the worst time, but it is a grind.
Checking calculations.
Auditing time and material bills.
Chasing down missing material delivery tickets.
Assembling final earthwork quantities.
Ugh….
Let’s Talk About Close-Out
As the job winds down, you start looking at the last stage of your project. You’re getting your punch list together. Maybe you’re cutting back on staff as members of your crew are reassigned. It’s a natural progression. Every job goes through it.
As construction engineers, our work product is paper. Sure, we guide the construction effort with our knowledge & skill sets. We facilitate work efforts. We trouble-shoot. We measure & pay for the work the contractor is constructing. We’re proud of being able to play an integral part in the project, but, the concrete, earth, aggregate & steel that was installed was done by the contractor’s work force.
Our work ends up in a bunch of bankers boxes.
And as painful as it is to say that, it is our work. Paperwork is our business. Job administration is what we do.
The saying goes:
The job has to look as good on paper as it does in the field.
That places a heavy burden on those of us who are responsible for producing it. It has to be accurate. It has to be complete. Auditable.
4 Tips for Project Close-Out
I’ve survived plenty of close-outs. I’ve been really lucky – Our crews are rock solid. Our documentation (not bragging, just saying) is always squared-away. Documentation auditors always enjoy reviewing our books because we keep things in order.
Project documentation is not an individual sport – It’s a team effort. It’s having systems that have been fire-tested, tweaked over the years and carried-out in a methodical process.
So here’s a few ideas that you can apply to your projects that will help your end-of-the-job work much easier.
1. Talk About Close-Out at the Start of Your Project
Consider this: Whey you are starting a task or a project or a chore around the house, preparation makes the production come together quicker than it would if you just jumped into a task feet first without thinking, right? Nobody, say, sealcoats their driveway without cleaning & sweeping it, sealing the cracks, filling-in any divots, taping-off adjacent concrete, etc. It’s planning. We’re in construction. Every operation starts with a plan (if you’re good, of course…).
Treat your job close-out as you would any other project:
Begin with the end in mind.
The best way to chart that course is to start talking about documentation and, yes, even close-out, right out of the gate. Why not talk about it early – Set the tone for the game. Get everyone on-board. That goes for you, your agency client, your contractor & subs, the utility carriers, everyone involved in the job.
It doesn’t have to be a long drawn-out discussion, either. Make it part of your precon meeting agenda. Look through your project. Have an idea of some of the “tougher close-out items” that you’ll need and mention those.
2. Assign “A Closer”
Certainly the analogy of a late-inning relief pitcher does well for this item – There’s no need for me to explain it.
Who is going to be the Go-To person on your crew who is going to pull everything together? Who is going to be responsible for going through, say, the agency-required list of final documents that you and your crew will be required to include in your job boxes?
You may have the luxury of having a full-time documentation engineer on your crew. Hallelujah. And if you are lucky enough to have a person in that role who has previously closed-out a project or two, you are in great shape.
But, what if you’re running the project by yourself? What if it’s you, one inspector and a materials engineer? You need to figure out who & how your crew is going to rally-up.
Start looking at your close-out deliverables and divide them up. Maybe your materials engineer will be responsible for assuring you have all of the material tickets & certs that you need, lab reports and field inspection records. That’s a good start.
Work your way through your list of pay items and chart a course.
3. Use Checklists
You guys know how I feel about checklists, right? Go back and read my article on using checklists for constructability reviews, or my article on pre-inspection safety briefs. I can’t live without checklists…
Checklists are vital.
If you are involved in government work, most agencies already have created checklists of the final documentation that is required to be turned-in. Print them out. Give them to everyone on your crew. Maybe schedule a lunch meeting with the crew to run through them, item by item. Not only will it expose your crew to the myriad of paperwork that is needed, but, it will serve as ticklers for them while they are working on site, allowing them to hopefully be looking ahead for paperwork & documentation that you’ll need later.
Say, for instance, you are on a concrete paving project, and one of the documentation requirements you have is depth checks of the concrete as it is cast to document that the proper thickness of pavement is being cast. How are you recording that information? Where are you housing the data. And how are you going to quickly retrieve it if an auditor asks you? By getting your whole crew thinking about it, when the time comes for paving, your field staff will be steps ahead already.
Below, I’m going to give you a few links to some Illinois DOT checklists. These might be samples for you if you work in other states, or maybe you work in the private sector where government forms aren’t required: Use these links & documents as guides to developing your own checklists.
IDOT Construction Memo 81 – District Construction Project File Requirements
IDOT Contract Finalization Procedure – Resident Engineer’s Checklist
IDOT BC 111 – Checklist for Engineer’s Final Payment Estimate
IDOT District 5 – Final Paper Checklist
IDOT District 5 – Checklist Prior to Final Audit
4. Train Your Crew to Always Finish It Now
One of the stumbling blocks that often occurs during the course of the project is pace – The contractor starts pushing the job, maybe long-shifting, working Saturday’s, running a couple of night shifts.
Your crew gets pushed. Your field engineers are getting measurements & tickets and trying to keep up, but you start seeing gaps. Slips.
The inspection reports start coming in with lesser information than the previous month. Maybe you’re seeing more estimated calculations & quantities: “Oh, don’t worry, Chief – We’ll run all the calc’s during winter close-out.”
And then what happens: Budgets get tightened. Staff gets reassigned. And guess who’s left trying to do the final computations that didn’t get done over the summer…??
Yep. It’s you.
There is NOTHING WORSE than having to clean up a mess, particularly when it’s not yours. But in the case of job documentation, well, it still is kind of your mess. You let it get there. You’re the RE. You’re in-charge.
Take my advice – Get your crew to final their quantities. Their audits. Their material ticket collections.
Look, we’re human. Time passes. We get busy. We forget things. We think we’ll be able to remember things, like measurements, or jobsite events. Maybe we figure we can reduce all of our survey notes once the job shuts down for the winter.
But what happens when we can recover missing information. Oh man, it’s a pickle you don’t want to have to deal with.
Make it happen. Push people to finish their work. Think of it this way – If they don’t finish it, there’s a high likelihood that you will. And believe me, that sucks…
After Actions
This article is a complement to Episode 10 of The Construction Engineering Show, where I put a voice to all of these ideas. Give it a listen.
I’ve got more close-out ideas, some that might be a little more “in the weeds” than this list here – Keep your eyes open for a follow-up article.
So be proactive. Stay ahead. Look for what you’ll need 6 months from now when there is snow on the ground and your boss wants to move you to your next project. The more you do on the front end in terms of preparing, the better your crew’s close-out work will be.
Be the first to comment