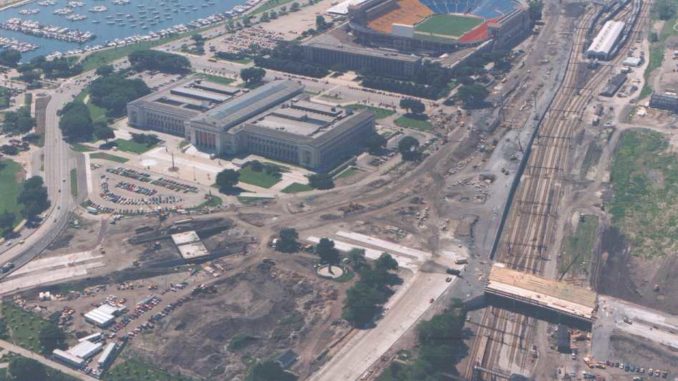
Our office was recently asked a question regarding the possible use of slag in a construction project. I decided to do a “shallow dive” into slag, its properties & uses insofar as construction in Illinois is concerned to see if I could shed any light on their issues.
Slag – What Is It?
Slag is a term that gets thrown around a lot but few really understand how many variations of the material there are. Most of us, when we hear the term “slag” think of steel production: Iron ore, coke and waste minerals are heated, and when the metals are separated, the resulting “waste product” is called slag. The slag, once it is cooled, either atmospherically or by being immersed in water, solidifies. Slag used to be a waste product that steel manufacturers had no use for, however, the slag can be processed and turned into a renewable material that can be used in a variety of construction materials.
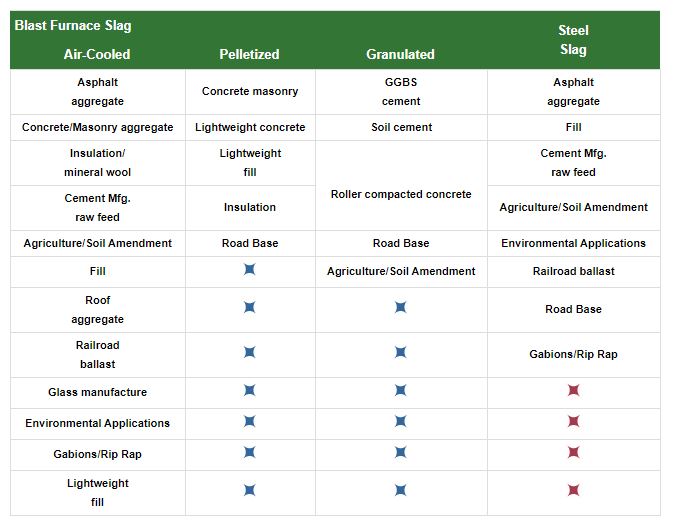
The multitude of slag uses is well-beyond the theme of this article. I’d like to take a look at 4 common heavy highway uses of slag.
1. Air-Cooled Blast Furnace Slag (ACBFS)
ACBFS is produced when the molted liquid slag is, as its name infers, is allowed to cool atmospherically. The cooled mass is then crushed to produce a graded aggregate.
ACBFS aggregate is hard and lightweight. Whereas limestone aggregates can have unit weights in the range of 120 pcf – 135 pcf, slag aggregates can have unit weights as low as 70 pcf. The fractured surfaces are typically angular which creates an aggregate that has high stability & friction angle characteristics.
One of the potential drawbacks to ACBFS is sulfur. When contacted with water for extended periods of time, the sulfurous compounds can be released, resulting in a highly-odorous greenish/yellowish leachate.
2. Ground Granulated Blast Furnace Slag (GGBFS)
GGBFS is a byproduct of steel production similar to ACBFS, but it is rapidly-cooled by water immersion. This rapid cooling produces a glassy, non-crystalline material that, when ground, produces cementatious-sized particles (rather than the aggregate-sized particles of ACBFS).
GGBFS is commonly used in concrete production as a cement replacement. It has a low heat of hydration characteristic that can provide advantages when constructing mass concrete structures reducing concrete temperature during the curing process.
3. Steel Slag
Steel slag is a byproduct of pig iron processing. Steel slag, once cooled, can be processed similar to ACBFS into aggregate-sized particles that are angular and very dense compared to natural aggregates.
Steel slag is used as a surface aggregate in HMA paving mixes. Its density and high frictional resistance characteristics provide increased durability beyond what natural aggregates can provide. Because it often-contains calcuim and/or magnesium, it can have a tendency to swell rapidly when exposed to moisture, making it an undesirable material for embankments and backfilling installations.
4. Wet-Bottom Boiler Slag (WBBS)
WBBS is not a by-product of steel or iron production, it is a by-product of coal burning in wet-bottom boilers. As coal is burned and ash is produced, the bottom ash is held in the bottom of the furnace in a molten liquid state. The material is somewhat durable, can be processed to a uniform size and blended with other fine aggregates.
WBBS is typically used as a roadway seal coat aggregate. It can also be used as a road salt additive to provide frictional resistance for roads during snow and ice conditions.
ACBFS Use in Roadway Construction
So the reason for my short dive into All Things Slag was this: What do the Illinois Department of Transportation (IDOT), the Illinois State Toll Highway Authority (ISTHA) and the Indiana Department of Transportation (INDOT) say about slag? And particularly, are the agencies allowing slag to be used in embankments, roadway subbases and for trench backfill.
As far as I can tell, the answer is “Yes” to all three, but, there are plenty of exceptions and caveats to go along with it. Let’s take a look at IDOT’s requirements.
IDOT Approved Uses of ACBFS
IDOT permits the use of ACBFS for several construction uses:
IDOT Policy Memorandum 9-08.2 CRUSHED SLAG PRODUCER CERTIFICATION notes that the production of slag-based aggregates follow a certification and self-testing program for crushed slag producers.
IDOT provides further specifications regarding ACBFS’s use for backfilling trenches. In its Supplemental Specifications and Recurring Special Provisions Adopted January 1, 2019, IDOT included its previously-issued
BDE Special Provision for STEEL SLAG IN TRENCH BACKFILL (BDE):
Looking at IDOT Article 1004.04 – COARSE AGGREGATES, the material specifications are as follows:
Personal Experience with Slag
I’ve been on 2 projects where slag was used: One was over 20 years ago, and one is currently being constructed. I’ll give you my takeaways on both.
Lake Shore Drive Relocation Around Solider Field
In 1996 I served as a Resident Engineer for the $45 million relocation of Lake Shore Drive around Soldier Field. It was monumental project, one that I am extremely proud and humbled to have worked on. The project moved the northbound lanes of Lake Shore Drive, which previously ran east of Soldier Field, to the west side, creating space for us to construct the Museum Campus.
One of the components of the project was constructing a reinforced earth wall between the relocated southbound LSD and the Metra/Illinois Central/South Shore Railroad tracks. The soils in this region of the City of Chicago were predominantly comprised of the debris & cinders left from the infamous Great Chicago Fire of 1871. The soils were extremely tender and prone to deep settlement. In order for the new embankments and retaining walls to be constructed, slag was specified as the retaining wall backfill due to its lower unit weight. (In the photo, below, you can see slag being placed in the foreground along the railroad tracks).
Our MSE wall straps were installed in the slag backfill: Current MSE wall spec’s typically no longer allow this. Given the proximity of the project to the Indiana steel mills, the material was readily-available. The installation of the MSE walls went very well. The walls remain functioning to this day.
Canadian Pacific / Grand Trunk Railroad Shoofly Siding – Munster, Indiana.
Our company has been providing construction support services to Canadian National Railroad for a project in Munster, Indiana. The town is constructing a new roadway underpass structure which will alleviate a congested intersection at 45th and Calumet Avenues.
Part of the project required the construction of a shoofly track to move the two active CN tracks away from the underpass excavation area. Slag is a plentiful material in Northwest Indiana: CN and the Town allowed the Contractor to use INDOT Grade 53 slag aggregate as the temporary embankment material for the shoofly. The material was delivered, placed and compacted in the same manner as natural aggregates. The shoofly was energized in October, 2019 and so far, the slag is performing as intended.
Close Out
So I’m running out of time: I did not have a chance to provide my research on ISTHA or INDOT use of slag, but from what I can tell, their uses are consistent with IDOT’s. Hopefully I’ll have time in the near future to edit this post and provide some insights.
I found some great resources in doing my technical dive: I’m providing links (below) if you are interested in reading more on this subject.
As always, feel free to reach out direct or comment: If anything I have provided in this article is contrary to you understanding, please let me know so that I can get any mis-information I’ve provided corrected.
Beemsterboer Companies – A Northwest Indiana Contractor & Slag Producer
FHWA – User Guidelines for Waste and Byproduct Materials in Pavement Construction
Be the first to comment